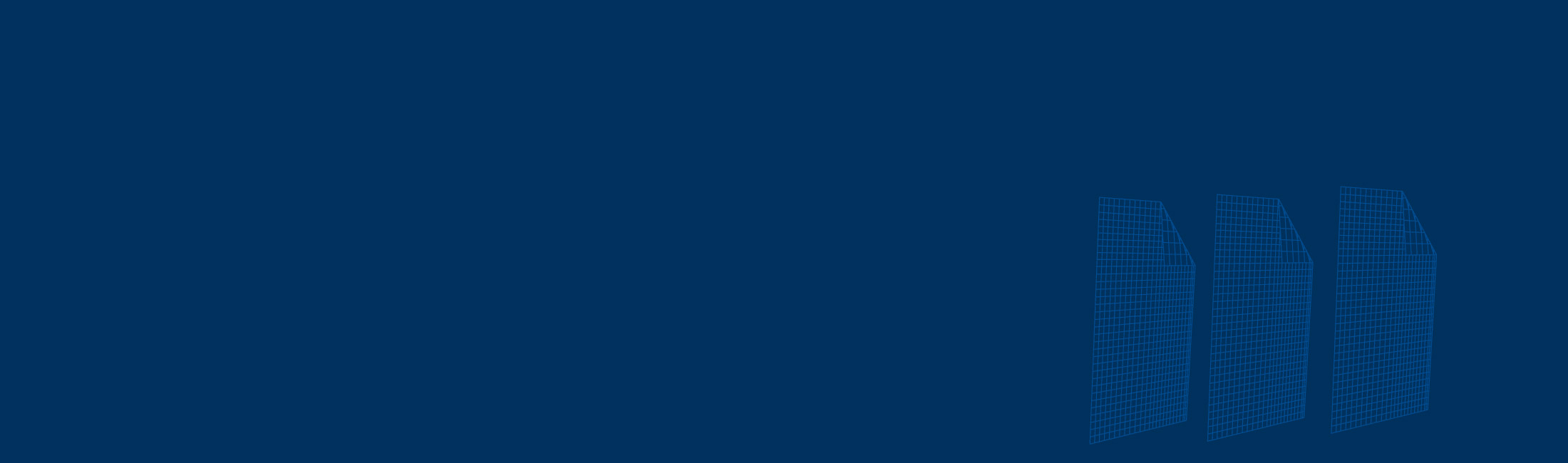
常见问题
有关使用 AGC 材料进行加工的常见问题解答
1. 层压板在多次高温暴露后是否出现任何变色效应或染色问题?
- 经过多次高温循环之后,每块层压板均会变暗。程度则取决于温度及循环持续时间。暴露于接近分解温度下的层压板比暴露于较低温度下的层压板会更暗。应注意的是,阻焊层的变色效应可能会掩盖底层基板的变化。
- 层压板在多次高温暴露之后通常不会染色,除非已被化学品所污染。某些水溶性助焊剂可能会导致染色,阻焊层经过某些助焊剂处理之后,将保持较高的离子污染水平。
2. 在组装过程中,AOI 是否存在与层压板相关的对比度问题?
- 如果层压板在组装过程中变暗,则不会对大多数 AOI 工序产生负面影响,因为这些检查通常依赖于阻焊层的对比度。
- 如果 AOI 对反射率和/或荧光起作用,则这些机制在很大程度上也不受颜色变化的影响。
3. 层压板是否会导致面板或成品板的翘曲量?层压板可通过多种方式导致 PCB 翘曲:
- 首先,这些电路板可能是利用不平衡的结构建造的。当电路板的设计层数为奇数或电路板中心平面的任一侧的电介质不平衡时,通常会发生这种情况。
- 其次,电路板可能具有平衡结构,但核心本身是不对称的,并且使用了不同风格的预浸料。例如,0.005 英寸的芯可以由单层 2116、双层 1080 或一层 2113 和 1080 制造而成。如果两个不同层的方向未正确分布在电路板的中心平面周围,则后一种结构可能会产生翘曲。
- 电路板/面板上的铜分布也可能导致翘曲。设计者应尽量平衡电路板中心周围的铜,以尽量减少翘曲。在层压过程中,制造商应采用通风模式,提供平衡的铜残留量,而不牺牲排出水分和空气的能力。
- 在 PCB 制造与组装阶段,将电路板暴露于高温之下可能会导致翘曲,尤其是在存在前后梯度的情况下。在多层的层压循环过程中也可能引起翘曲。这也可能发生在电路板车间的 HASL 或组装时的回流焊过程中。在回流焊时,工艺面板厚度、面板尺寸及组件重量会影响翘曲。
4. 层压板的热膨胀系数是多少?它对组装过程有什么影响?热膨胀系数是因温度变化而引起的尺寸变化。
- 每块层压板在 X、Y 和 Z 轴上可能具有不同的热膨胀系数 (CTE)。X 和 Y 轴上的 CTE 受所用增强材料的影响最大。对于由 E 玻璃制成的电路板,CTE 通常为 12-16 ppm/℃。
- Z 轴 CTE 也很重要。当一块电路板在 X 轴和 Y 轴上受到增强材料约束时,它会在受热时在 Z 轴上移动。在通常情况下,我们将这些差异报告为当电路板的温度从 50 ℃ 升高到 288 ℃ 时膨胀的百分比变化。膨胀量取决于电路板的设计、树脂含量的类型以及增强材料。可以预计,膨胀范围将从 1.5% 的低点延伸到近 7% 的高点。由于显而易见的原因,不希望在高层数和/或厚板上出现高 Z 轴扩展。否则,可能会在热循环过程中引发可靠性问题。典型缺陷可能包括孔壁镀层断裂、分层等。
5. 波峰焊对层压板有什么影响?
- 如果工序控制得当,波峰焊对层压板的影响很小。
- 需要考虑水分吸收以避免分层,因此建议在波峰焊之前进行烘烤。
6. 在线/离线清洗过程中对电路板或面板有什么影响?
- 在一定时间内,裸层压板会比成品板(即覆盖有阻焊层的电路板)吸收更多的水分。此外,电路板/面板的清洗频率和清洗时间也会影响每块层压板的水分吸收。
- 如果直接进行加工,正确储存的层压板进行短时间清洗通常是没有问题的。
- 检查化学电阻率(皂化剂、丙酮等)
7. 层压板对水分的敏感性如何?
- 层压板吸收的水分量取决于温度、湿度及工序持续时间。我们通常利用标准 IPC 规范对层压板进行测试。
- 还应注意的是,每个层压板系列具有不同的吸水率。这是一个关键点,因为在回流焊或波峰焊等高温偏移过程中,有必要延长某些层压板的烘烤时间,以去除可能导致分层的水分。
8. 电路板(层压板)多久可以重工一次?
- 电路板可承受的重工量取决于几个因素。使用的材料类型是明显的关键因素,但铜剥离强度、热量、机械力、焊盘尺寸、元件尺寸、元件重量、铜分布、结构和厚度等因素也很重要。
- 为了减少重工引起的问题,应根据产品资料中规定的属性对层压板进行处理,尤其是最高热暴露温度(回流焊、波峰焊和手工重工)。
- 具有低 CTE 和高热可靠性(根据玻璃化转变温度 (Tg) 和分层时间(T260、T288 或 T300)测定)的层压板在多个重工周期中性能更佳。
9. 层压板可暴露的最高温度和持续时间是多少?
- 应根据产品资料中规定的属性对层压板进行处理,尤其是最高热暴露温度(回流焊、波峰焊和手工重工)。
- 不过,暴露时间和电路结构等某些因素可能会影响最高使用温度。如果存在这些因素,重要的是要考虑 RTI(相对热指数)和 MOT(最高工作温度)以获得最佳结果。
10. 层压板可以经受多少次温度循环?
- 层压板将伴随每次施加的热循环而降解。温度越接近热分解温度,降解过程越快。即使在较低温度下,降解仍在进行,只是速度较慢。
11. 剥离强度何时影响重工?焊盘多久可以重工一次?所需温度是多少?
- 重工要求取决于几个因素,例如铜剥离强度、施加的热量、机械力、焊盘尺寸以及具体的重工工序。
12. 层压板耐化学性的重要性是什么?
- 耐化学性对于清洁电路板(清洁、免清洁助焊剂)非常重要。在清洗工序中添加某些化学品可能会导致性能损失。电路板经常被污染,而人眼无法发现。此类污染可能导致现场故障,应予以避免。使用在线/离线清洁时,仔细考虑使用的任何清洁化学品变得极为重要。一般而言,去离子水和酒精是很好的解决方案。
13. 层压板属性如何影响组装过程中的刻槽或断裂相关问题?
- 在某些时候,部分面板必须分解成板。根据面板尺寸、厚度、重量、组装面板的总重量或刻槽深度,断裂会使组装过程更具挑战性。
- 某些层压板在受热后比其他层压板更柔软,这会影响面板的稳定性。对于特定的面板尺寸和/或厚度,可能需要确定特定的处理程序(例如用于放置的中间支撑物、回流焊工序等)。通常,我们建议审查机械性能,以确定是否需要采用额外的处理程序。
14. 组装过程中分层的根本原因是什么?
- 分层的根本原因通常是压力机中的低压、层压板的水分吸收、预浸料或芯表面的污染(油、油脂等)、阻焊塞孔中的残留水分、固化不足的层压板、未优化的氧化物以及去钻污化学成分。
- 最薄弱的粘合环节通常是氧化铜表面和预浸料之间的界面。大多数分层发生在此界面上。修订版 02-21
- 通常在组装环境中,水分吸收与高温循环结合可能导致分层。
- 通常,具有高 Tg、高分解温度、低 Z 轴 CTE 的层压板以及具有良好 T260、T288 或 T300 性能的层压板更适合多次高温循环。
15. 哪些层压板可用于无铅焊接?
- 至于特定材料是否无铅兼容,电路板制造工序的细节起着非常重要的作用。镀铜厚度以及 PCB 中残留的水分含量是需要考虑的诸多因素中的两个。
- 在高温、无铅组装过程中,认识 HDI 设计属性非常重要。例如 PTH 尺寸、孔到孔距离、层数等也会影响产品性能。
- 除了一些非常陈旧的材料等级外,所有 AGC层压板和预浸料均与无铅焊接兼容,具体取决于设计和回流焊条件。
16. 印刷电路制造与组装
- 成品印刷电路板 (PCB) 的储存对于其在下游加工中的生存能力至关重要,不应被忽视。当今市场上有许多不同的树脂体系,每一种均以不同的速率吸收水分。
随着 RoHS 倡议的实施以及无铅焊料(SnPb 至 SAC305)使用的增加,该行业已转向更高的回流焊温(220℃ – 260℃),由于组装需要在更高温度下进行,吸收水分的蒸汽压大大增加。在 SMT 或波峰焊之前,如果未去除这种较高的蒸汽压,可能导致 PCB 分层或开裂。为限制水分吸收,建议将制造好的 PCB 装在经过批准的防潮袋中进行运输,该防潮袋可提供一层 ESD 保护。
确定哪种封装最适合制造的电路板取决于诸多因素。其中包括但不限于 PCB 的储存条件、层压材料、最终电镀表面光洁度以及电路板整体厚度。添加干燥剂包和氮气将有助于最大程度地减少水分吸收,并保持可焊接电路板的表面光洁度。包装内包含湿度指示卡,打开包装后可提供视觉证据。
引入氮气之后,应立即使用适当的热封设备将防潮袋密封。防潮袋打开后,应限制暴露于露天环境,以限制吸收水分。根据 JEDEC-STD-033 标准,如果防潮袋存放在不超过 400℃、相对湿度不超过 90% 的储藏室环境中,则干燥包装应能在长达 1 年的使用期限内限制水分吸收。
对于在含铅和无铅焊接工序下运行的 PCB,建议进行烘烤,以获得最佳性能和可靠性。不过,您应该咨询您的化学品供应商,以确保烘烤不会对可焊性产生不利影响。如前所述,不同的树脂体系会以不同的速率吸收水分(聚酰亚胺树脂是应特别注意的一种)。PCB 的设计、布局及金属表面处理在确定所需烘烤时间方面发挥着作用。例如,如果可行的话,一块各个表面均经过电镀的电路板可能需要很长时间的烘烤,才能去除任何残留的水分。
组装前,建议在对流烤箱中对电路板进行*机架烘烤,以允许适当的空气流动。以下是确定去除 PCB 中残留水分所需最短烘烤时间的指南。可能需要更长的烘烤时间,但可能会对可焊性产生不利影响:
OSP/沉锡:在 110℃-120℃ (230℉ – 250℉) 下 1-2 小时
ENIG/沉银:在 150℃ (300℉) 下 4-6 小时
*PCB 应放置在机架上,不得相互堆叠。处于堆叠之中的电路板可能无法看到允许适当去除水分的最低温度。
如要实现高可靠性的成品 PCB,经过适当设置和校准的回流焊炉以及任何手工焊接操作至关重要。日后需要进行二次或后焊加工的电路板应储存并重新密封于适当的防潮袋或氮气柜中。
本文档所包含的信息被视为准确可靠。不过,有许多因素可能会影响最终结果,个人客户可自行确定哪些工序最适合自己的制造作业,以生产出具有高度可靠性的组件。